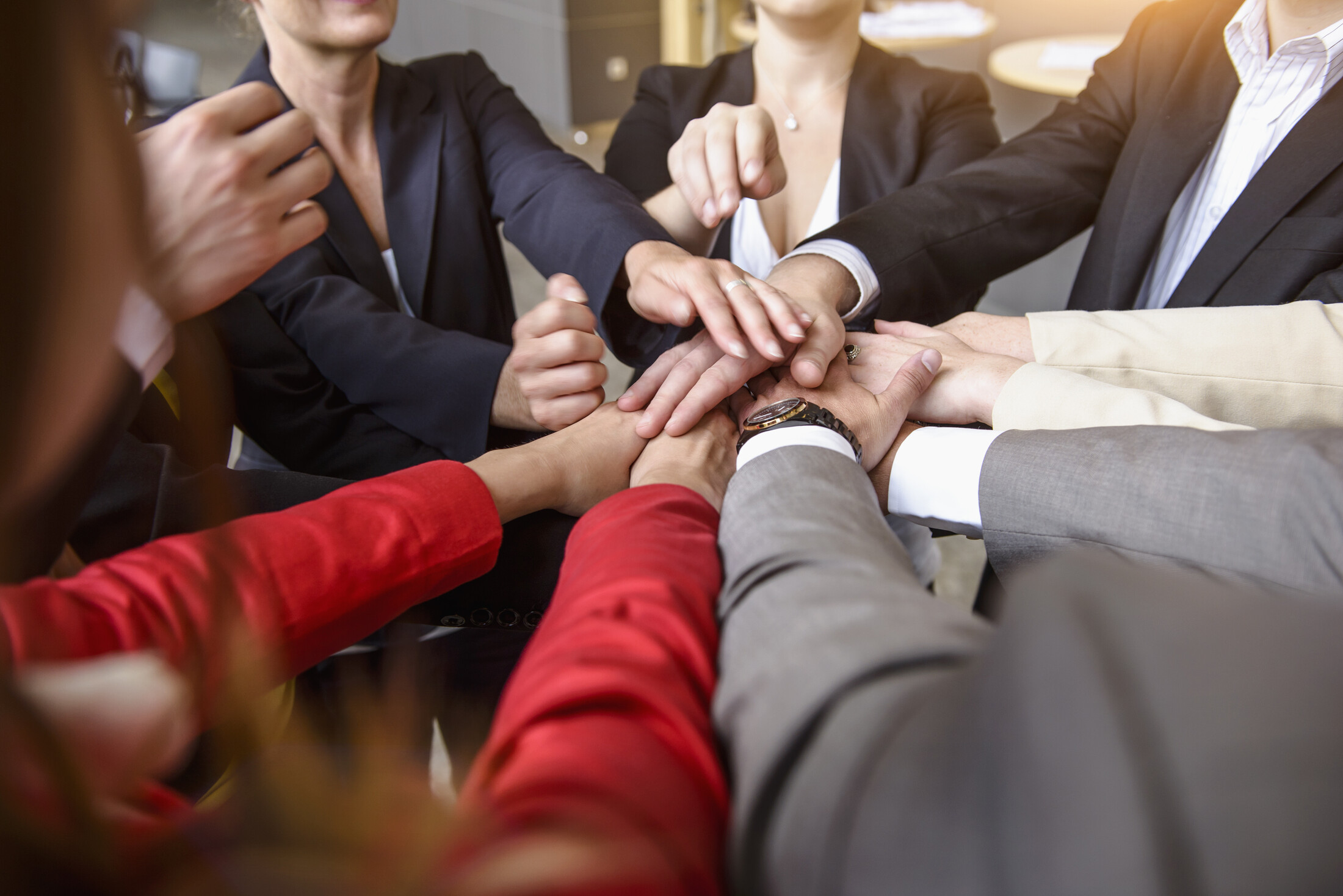
2025 marks an extraordinary milestone for HTM SRL: 30 years of success in the design and production of molds for plastic injection and aluminum die casting. Since 1995, HTM – High Technology Mould has charted a path of innovation, quality, and precision, establishing itself as a point of reference in the sector at an international level.
A Path of Growth and Innovation
Since its foundation, HTM SRL has pursued excellence through the use of advanced technologies and a highly qualified team. Thanks to our constant attention to quality and precision, we have been able to meet the needs of customers operating in different sectors, including:
- • Automotive
- • Aerospace
- • Food industry
- • Medical sector
- • Industrial mechanics
- • Electronics and mechatronics
- • Consumer goods and luxury
The integration between plastic injection and aluminum die casting is one of our main strengths, allowing us to offer complete and optimized solutions for industrial production.
What Makes HTM SRL Unique?
Over the years, HTM SRL has consolidated its position thanks to a set of distinctive values and skills:
- • Quality and precision: We use advanced analysis tools such as Moldflow to ensure maximum efficiency and accuracy in mold production.
- • Customization and co-design: We work closely with customers, offering tailor-made solutions through a highly collaborative co-engineering process.
- • Cutting-edge technologies: We use state-of-the-art machinery compliant with Industry 4.0 and 5.0 standards, ensuring high automation and total control over production processes.
- • Reliability and after-sales support: We offer maintenance and technical assistance services to ensure maximum efficiency and durability of molds over time.
- • Sustainability: We are committed to reducing environmental impact with optimized production processes and innovative materials.
Our Services
To ensure maximum support for our customers, HTM SRL offers a complete range of services:
- • Custom mold design and production
- • Research and development (R&D) and co-design
- • 3D prototyping
- • Sampling and production start-up
- • Maintenance and technical assistance
- • Specialized consulting
- • Production monitoring and spare parts management
Looking to the Future: Innovation and Continuous Growth
This 30-year milestone represents for HTM SRL not a point of arrival, but a new beginning. We continue to invest in cutting-edge technologies and in the training of our team to face the challenges of the future with the same passion and dedication that have brought us this far.
We are proud of our journey and grateful to our customers, partners, and collaborators who have contributed to our success. The future of HTM SRL will be marked by new ambitious goals, with the same determination that has allowed us to grow and innovate over these three decades.
Thank you for being part of our story. The best is yet to come!